Most people haven’t heard of the engine created by Felix Wankel in the 1960s, but its derivatives may end up powering the military’s future unmanned aerial vehicles.
Despite a compact design that allows it to run at higher speeds and produce more power than conventional internal combustion engines, the Wankel engine never really caught on.
It’s bad on fuel efficiency, and it burns too much oil.
But now, engine technology company LiquidPiston Inc. may have changed that, and they want to throw their new design into military drones.
Company CEO Alec Shkolnik has a Wankel engine design that’s essentially been inverted, and he says it can increase flight endurance by more than 50 percent — the maximum length of time that an aircraft can spend in cruising flight.
“We developed what we call the X4 engine, which is like the old Wankel rotary engine, but flipped inside out,” Shkolnik said. “It solved a lot of the challenges the Wankel used to have while giving it this new thermodynamic cycle upgrade.”
In addition to the advanced flight time, LiquidPiston’s propulsion can reportedly reduce a drone’s engine heat signature and minimize vibration impact on sensitive intelligence, surveillance, and reconnaissance equipment.
The Defense Advanced Research Projects Agency, or DARPA, is certainly interested. The government agency just awarded LiquidPiston another $2.5 million to develop and refine its 30 kilowatt, 40 horsepower X4 rotary diesel engine prototype.
“DARPA believes that there is potential for a family of high-efficiency, compact, lightweight heavy-fuel engines,” Mark Gustafson, a DARPA program manager, said.
“If fully successful, this project will provide proof of concept that our challenging objectives are achievable and pave the way for potential new capabilities in ground, air, and maritime applications,” he added.
Combined with previous funds from 2016, DARPA has pushed $6 million into the new technology.
Here’s how it works: The regular Wankel engine replaces pistons with triangular rotors that follow an elliptical path around an oval-shaped chamber. Combustion then occurs in the space between the triangular and circular shapes.
LiquidPiston inverted that design.
The X4 engine uses an oval rotor in a triangular chamber. Combustion occurs at fixed points within the chamber, which makes it easier to lubricate without burning oil.
By doing it this way, the company says it has engineered the first new combustion engine and engine cycle in more than 80 years. LiquidPiston’s design can be five to 10 times smaller than a normal piston engine — as small as an iPhone — lighter than a diesel engine, and two times more efficient than a gasoline engine.
On top of that, an electric vehicle using a LiquidPiston engine combined with a small battery pack could have a lower carbon dioxide footprint than plug-in electric vehicles.
DARPA gave the company the most recent investment after they proved the feasibility of their design.
“The targets are extremely aggressive,” Shkolnik said. “The engine should weigh 30 to 40 pounds and double the efficiency compared to other engines, for example the Army’s Shadow UAV.”
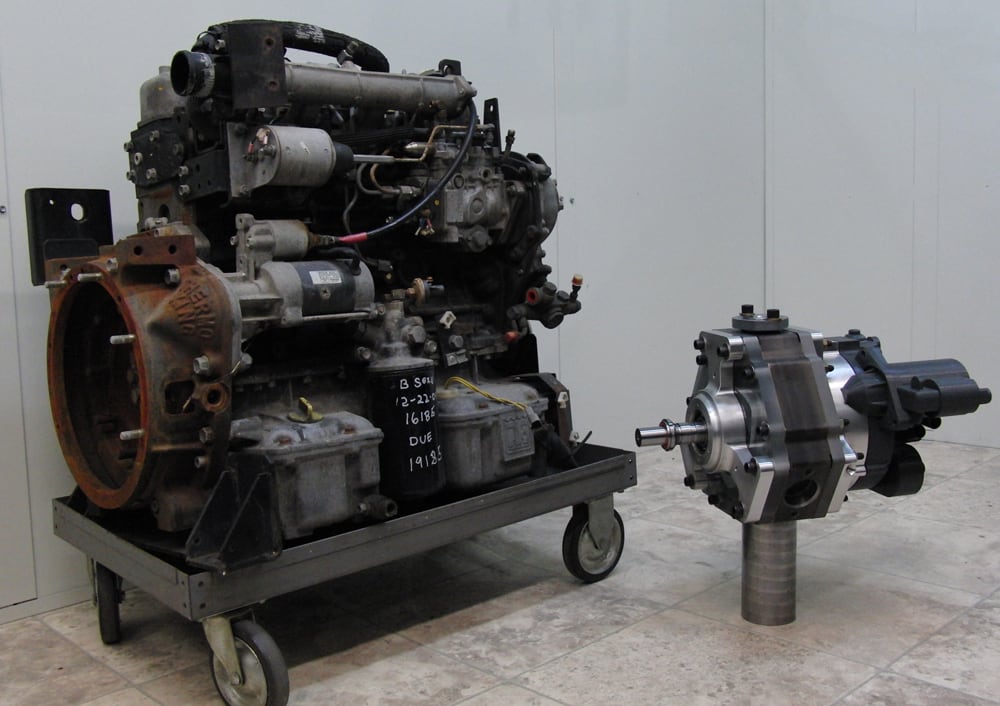
The Army’s RQ-7 Shadow — a drone with a 20-foot wingspan and 18,000-foot ceiling — currently uses a Wankel engine design and has a flight time of four to nine hours, depending on payload and variation.
Another important factor is that the X4 technology is scalable.
“We have a 5 horsepower engine as well, which could fit in something like an Aerosonde [a 30-pound UAV],” Shkolnik said. “This 40 horsepower one is more suited for the Shadow, or drones of similar size.”
“The Shadow, though, is something we talked about with DARPA because it’s a well-known platform, its got more than a million hours of operating time, and it’s really not a good engine on that bird,” Shkolnik added. “It’s one of the big limiting factors for that platform.”
The Shadow’s engine has had issues scattering the enemy due to the engine’s excessive noise, which is like a “flying lawn-mower,” Shkolnik said.
RELATED
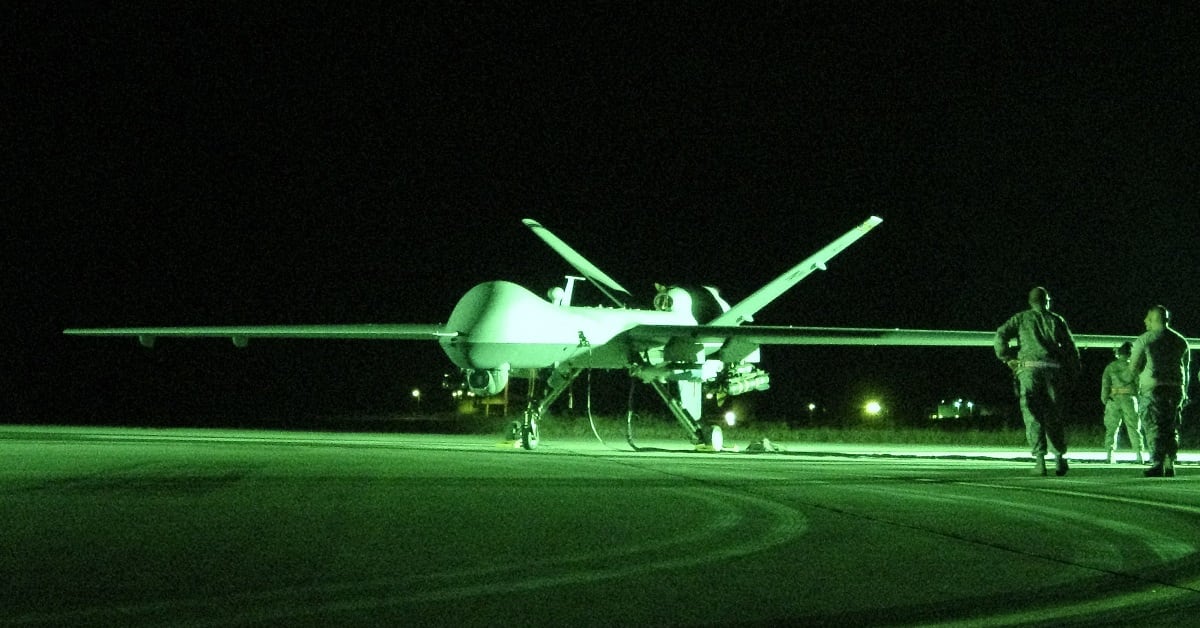
“Our engine has the potential to be very quiet,” he added. “There’s no piston slap, for instance, so the only real noise is from the gears and combustion. So, it’s relatively quiet.”
Because the X4 will be a pure diesel engine and not spark ignited, LiquidPiston can also design variants that have no electronics on board that could interfere with certain types of surveillance equipment. The rotary engine design also decreases engine vibration that could throw off measurements.
On top of that, because the engine is thermally more efficient, less heat goes into the exhaust, so it should have a lower heat signature to bypass an enemy’s thermal imaging devices.
“The other thing I want to point out is the reliability and durability, because that’s a big limiting factor for today’s UAV engines,” Shkolnik said.
The Army’s Shadow drones have difficulties starting and are often lost in mishaps, he said. Their current engine has to be serviced frequently.
“Because our engine is an inside-out version of the Wankel rotary, our seals aren’t in the rotor, they’re actually in the housing and they’re much easier to lubricate,” Shkolnik added.
The engine is entering its second phase of testing this year, which should wrap up around October. The objectives are to demonstrate the 30 kilowatts of power and to reach 45 percent fuel efficiency. That development will be executed at LiquidPiston’s test facility in Connecticut.
After the second phase, LiquidPiston plans to team up with a transition partner company that makes UAVs to bring the design to life.
Kyle Rempfer was an editor and reporter who has covered combat operations, criminal cases, foreign military assistance and training accidents. Before entering journalism, Kyle served in U.S. Air Force Special Tactics and deployed in 2014 to Paktika Province, Afghanistan, and Baghdad, Iraq.